Marine construction is a complex and challenging field that demands materials capable of withstanding harsh underwater environments. From offshore platforms to luxury yachts, hardware components play a pivotal role in ensuring the safety, functionality, and aesthetics of marine structures. In this blog article, we delve into the world of metalwork in marine construction, exploring the essential hardware parts that are polished, buffed, plated, or smithed to meet the unique demands of this industry.
1. Marine Hardware Polishing:
Polishing is a crucial process for marine hardware components as it not only enhances their appearance but also helps to create a smooth, corrosion-resistant surface. Stainless steel marine hardware, such as cleats, hinges, and handrails, undergo meticulous polishing to remove imperfections and achieve a mirror-like finish. Polished hardware not only adds a touch of elegance to marine structures but also minimizes the risk of rusting and corrosion, ensuring longevity and durability in the challenging marine environment.
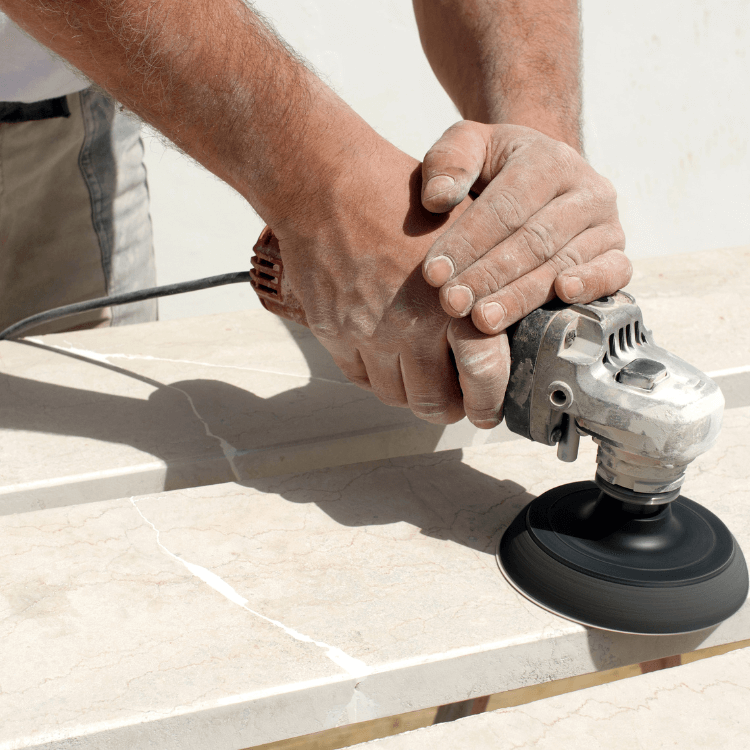
2. Buffing for Lustrous Appeal:
Buffing is another metalworking technique widely used in marine construction to achieve a gleaming and refined finish. Brass hardware parts, such as portholes, latches, and decorative accents, are carefully buffed to unveil their inherent shine and impart a touch of luxury to marine vessels and structures. The buffing process not only elevates the aesthetic appeal but also provides a protective layer against the corrosive effects of saltwater, making it an indispensable step in creating beautiful and functional marine hardware.
3. Marine Hardware Plating:
Metal plating is an essential aspect of marine construction, as it fortifies hardware components against the harsh marine environment and provides a range of benefits. Marine-grade chrome plating, for instance, is applied to various components like shafts, propellers, and fittings to enhance corrosion resistance and reduce friction, thus improving the overall performance and efficiency of marine vessels. Travis from Hollywood Marine Construction only uses corrosion resistant hardware when building docks, seawalls, and any other structures on or near the water. “There’s no way I would ever use hardware that wasn’t able to resist the corrosive forces you encounter when you’re near the sea. We’ve always used hardware that will last a long time like zinc coated fasteners.” Additionally, plating options like nickel and zinc provide protective coatings, ensuring long-lasting performance even in saltwater conditions.
4. Metal Smithing for Custom Marine Hardware:
While mass-produced hardware parts serve many marine construction needs, there are instances where custom-made components are required to suit specific vessel designs or restoration projects. Metal smithing comes to the fore in such cases, as skilled artisans use traditional forging and shaping techniques to create one-of-a-kind marine hardware pieces. Custom smithed hardware, such as decorative railings, personalized nameplates, and intricate fittings, not only add a touch of individuality but also showcase the enduring artistry of metalworking in marine construction.
The world of metalwork in marine construction is an exquisite blend of artistry and functionality, with each polished, buffed, plated, or smithed component contributing to the safety, performance, and beauty of marine structures. From the majestic luxury yachts to the resilient offshore platforms, docks, and piers, the attention to detail in metalwork ensures that marine hardware stands the test of time and harsh marine conditions. As advancements in metalworking techniques continue to evolve, we can expect to see even more innovative and sustainable solutions that further elevate the strength and allure of marine hardware in the years to come.